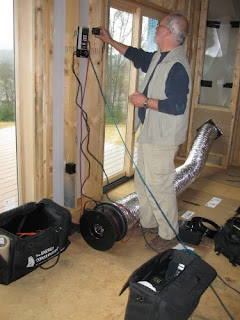
We hired Bruce Glanville of the Knox Housing Partnership to rate our home. The image here is Bruce conducting a "Duct blaster" test to determine how well our HV/AC duct system is sealed. It's a measure of how much of the air conditioning and/or heat leaks out into the unconditioned attic. The HERS rating also looks at the insulation system, the heating system selection, the amout of glass and its emissivity (E-factor), the solar gain, and the efficiency of appliances. At the preliminary rating estimate in November we scored a 62. That's a darn efficient design! Sweet! This preliminary rating was also very timely.
We've agonized a bit lately over the insulation system to choose. Our spec has called for open cell foam insulation throughout, but that is a very expensive choice. Our builder has proposed a hybrid "flash and batt" system where we use a thin layer of foam to seal the entire building envelope and provide a bit of insulation (R= 7), but then fill the rest of the wall cavity and attic with conventional fiberglas batts and blown cellulose. The flash and batt proposal will save us over 60% of the insulation cost. It turns out... the full foam system, while exotic and fun to talk about, doesn't really gain us any energy efficiency to speak of. Our projected HERS rating doesn't change at all with the more expensive insulation! Well... suddenly, the decision was made easy. Flash and batt started the next day at a savings of almost $14,000!
Once I find my camera, I'll post a few images of the insulation system being installed. It's pretty cool.